Essential Maintenance Tips for Insulated Steel Pipes in Cryogenic Facilities
Jul 20,2025
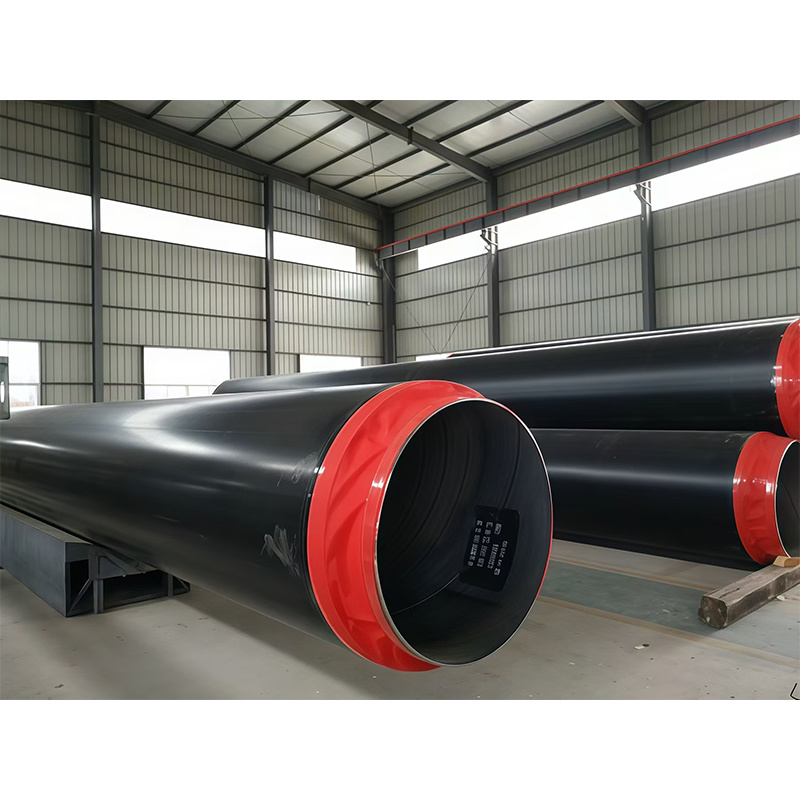
Essential Maintenance Tips for Insulated Steel Pipes in Cryogenic Facilities
Table of Contents
- Introduction to Insulated Steel Pipes in Cryogenic Applications
- Understanding Cryogenic Systems
- The Importance of Insulated Steel Pipes
- Routine Inspection Protocols for Cryogenic Pipes
- Preventive Maintenance Techniques
- Common Issues and Their Solutions
- Safety Considerations in Maintenance
- Conclusion
- FAQs about Insulated Steel Pipes in Cryogenic Facilities
Introduction to Insulated Steel Pipes in Cryogenic Applications
In the realm of cryogenic facilities, insulated steel pipes play a pivotal role in the transportation of liquefied gases at extremely low temperatures. Understanding the unique challenges associated with maintaining these pipes is crucial for ensuring the safety and efficiency of operations. Regular maintenance and inspection are not merely best practices; they are fundamental to preventing catastrophic failures that could arise from neglect.
Understanding Cryogenic Systems
Cryogenic systems operate at temperatures below -150°C (-238°F), making the choice of materials and maintenance practices critical. Insulated steel pipes are commonly used due to their strength and ability to retain thermal integrity. These systems are typically employed in industries such as LNG (Liquefied Natural Gas), aerospace, and medical applications. Understanding the physics behind cryogenics helps in developing effective maintenance strategies.
The Role of Insulation in Cryogenic Systems
Insulation is essential in cryogenic applications as it minimizes heat transfer, thereby maintaining the low temperatures required for safe and efficient operation. Insulated steel pipes usually feature multiple layers of insulation, including polyurethane foam or vacuum insulation, which significantly enhance their thermal performance. Regular assessment of the insulation integrity is vital, as breaches can lead to increased energy costs and safety risks.
The Importance of Insulated Steel Pipes
Insulated steel pipes are fundamental to the reliability of cryogenic systems. They not only provide structural support but also contribute to energy efficiency and safety. The insulation safeguards against the risk of condensation, freezing, and subsequent pipe damage, which can lead to system failures and costly downtime. Therefore, proactive maintenance is not just beneficial; it is essential for operational continuity.
Routine Inspection Protocols for Cryogenic Pipes
Establishing robust inspection protocols is critical for identifying potential issues before they escalate. The following routine checks should be performed:
Visual Inspections
Conduct visual inspections to identify any obvious signs of wear, damage, or corrosion on the pipe surface and insulation. Look for cracks, dents, or bulges that may indicate structural weaknesses.
Thermal Imaging
Utilize thermal imaging technology to detect heat loss in the insulation material. This non-invasive method enables the identification of areas that may require additional maintenance or repair.
Pressure Testing
Regular pressure testing of the insulated steel pipes is essential to ensure they can withstand their operational pressures. This process helps in detecting leaks and weaknesses in the system.
Preventive Maintenance Techniques
Implementing preventive maintenance techniques can significantly extend the lifespan of insulated steel pipes and enhance their performance.
Regular Cleaning and Maintenance
Keeping the pipes clean from external contaminants, such as dust and debris, is vital. Regular cleaning schedules should be established to prevent corrosion and degradation of the insulation materials.
Insulation Integrity Checks
Regularly assess the insulation for any signs of moisture ingress or degradation. Replacing damaged insulation material promptly can prevent more significant issues down the line.
Documentation and Record-Keeping
Maintain detailed records of all inspections, maintenance activities, and repairs. This documentation is invaluable for tracking the performance of the pipes over time and identifying recurring issues.
Common Issues and Their Solutions
Understanding common issues that arise within insulated steel pipes in cryogenic facilities is crucial for effective maintenance.
Corrosion
Corrosion is one of the most significant challenges faced by insulated steel pipes. It can occur due to moisture ingress or chemical exposure. To mitigate corrosion, ensure that protective coatings are intact and consider using corrosion-resistant materials. Regular inspections will help identify early signs of corrosion for timely intervention.
Insulation Failure
Insulation failure can lead to significant thermal losses and increased operational costs. If insulation materials show signs of wear, they should be replaced immediately. It is crucial to use high-quality insulation materials specifically designed for cryogenic applications.
Leakage
Leaks can be detrimental to the efficiency of cryogenic systems. Conduct routine pressure tests and visual inspections to detect and repair leaks promptly. Utilizing advanced sealing technologies can also help in preventing leaks.
Safety Considerations in Maintenance
Safety should always be a priority when working with insulated steel pipes in cryogenic facilities. Follow these key safety guidelines:
Personal Protective Equipment (PPE)
Ensure all personnel involved in maintenance activities wear appropriate PPE, including gloves, goggles, and thermal protective clothing, to safeguard against exposure to cryogenic materials.
Emergency Protocols
Establish clear emergency response protocols in case of accidents or leaks. Regular drills should be conducted to ensure all staff are familiar with the procedures.
Training and Certification
Provide continuous training for maintenance personnel on the specific requirements and hazards associated with cryogenic systems. Certification programs can enhance their skills and knowledge.
Conclusion
Maintaining insulated steel pipes in cryogenic facilities is a critical task that demands attention and expertise. By adhering to the essential maintenance tips outlined in this guide, operators can effectively mitigate risks, enhance the longevity of their systems, and ensure the safe transportation of cryogenic materials. Regular inspections, preventive maintenance, and a strong focus on safety considerations are paramount to achieving operational excellence in cryogenic applications.
FAQs about Insulated Steel Pipes in Cryogenic Facilities
1. What types of insulation are best for cryogenic applications?
High-performance insulation materials, such as polyurethane foam and vacuum insulation, are typically recommended for cryogenic applications due to their low thermal conductivity and resistance to moisture ingress.
2. How often should I perform maintenance on my insulated steel pipes?
Routine inspections should be conducted at least quarterly, while more comprehensive maintenance checks can be scheduled annually or biannually, depending on the operational conditions.
3. What are the signs that my insulated steel pipes need maintenance?
Signs may include visible corrosion, insulation wear, changes in pressure readings, and unexpected temperature variations in the cryogenic fluids being transported.
4. Can I repair insulation damage myself?
While minor insulation repairs may be performed by trained personnel, significant damage should be assessed and repaired by professionals to ensure compliance with safety standards and proper installation.
5. Are there any technologies available to help monitor insulated pipes?
Yes, advanced technologies such as thermal imaging cameras, ultrasonic leak detectors, and pressure monitoring systems can greatly assist in the ongoing monitoring and maintenance of insulated steel pipes in cryogenic facilities.
TAG:
Previous:
Related Posts
Essential Maintenance Tips for Insulated Steel Pipes in Cryogenic Facilities