Protect Your Infrastructure: The Comprehensive Benefits of Plastic-Coated Pipelines
Jul 26,2025
Protect Your Infrastructure: The Comprehensive Benefits of Plastic-Coated Pipelines
Table of Contents
1. Introduction to Plastic-Coated Pipelines
2. What Are Plastic-Coated Pipelines?
3. Advantages of Plastic Coating in Pipelines
3.1 Corrosion Resistance
3.2 Cost-Effectiveness
3.3 Environmental Sustainability
3.4 Improved Flow E
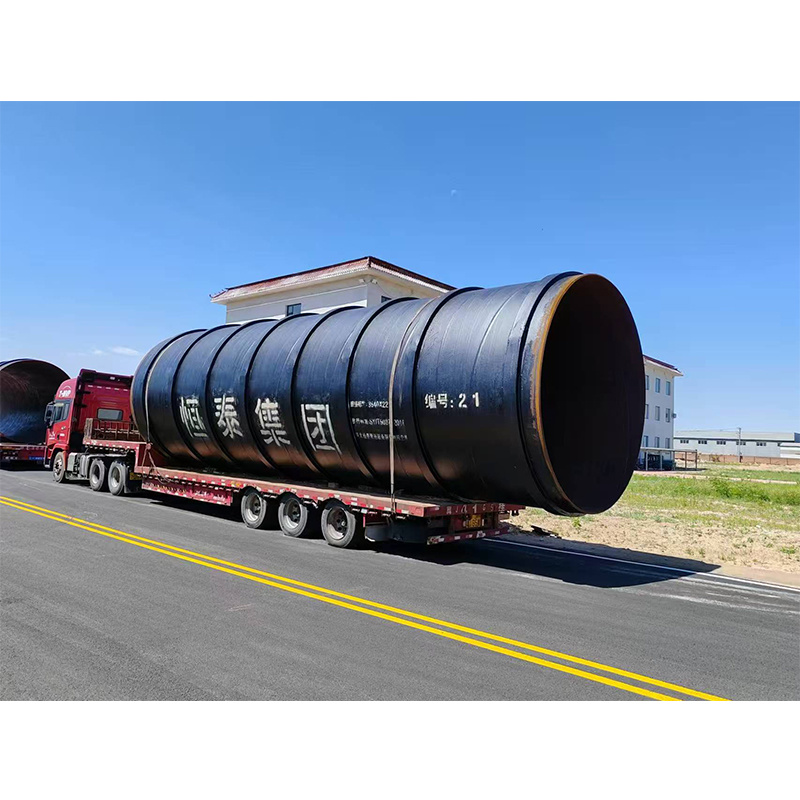
Protect Your Infrastructure: The Comprehensive Benefits of Plastic-Coated Pipelines
Table of Contents
- 1. Introduction to Plastic-Coated Pipelines
- 2. What Are Plastic-Coated Pipelines?
- 3. Advantages of Plastic Coating in Pipelines
- 3.1 Corrosion Resistance
- 3.2 Cost-Effectiveness
- 3.3 Environmental Sustainability
- 3.4 Improved Flow Efficiency
- 4. Applications of Plastic-Coated Pipelines
- 5. Maintenance and Care of Plastic-Coated Pipelines
- 6. Choosing the Right Pipeline Systems
- 7. Frequently Asked Questions
- 8. Conclusion
1. Introduction to Plastic-Coated Pipelines
In the realm of industrial infrastructure, **resilience** and **efficiency** are paramount. As industries face various challenges, ranging from corrosion to environmental regulations, the demand for innovative solutions has never been greater. **Plastic-coated pipelines** have emerged as a leading option for improving the longevity and performance of piping systems. In this article, we will delve into the numerous benefits of plastic-coated pipelines and how they can enhance your infrastructure.
2. What Are Plastic-Coated Pipelines?
Plastic-coated pipelines consist of traditional metal pipes that are enveloped in a layer of plastic material. This coating acts as a protective barrier against external elements. The most commonly used materials for coating include polyethylene, polypropylene, and PVC. These materials not only protect against corrosion but also offer several other advantages, making them ideal for various applications.
3. Advantages of Plastic Coating in Pipelines
3.1 Corrosion Resistance
One of the primary benefits of plastic-coated pipelines is their exceptional **corrosion resistance**. Traditional metal pipes are prone to rusting and degradation when exposed to moisture, chemicals, or extreme temperatures. In contrast, plastic coatings form a robust barrier that prevents direct contact between the metal surface and damaging elements. This significantly extends the lifespan of the pipeline and reduces maintenance costs.
3.2 Cost-Effectiveness
Investing in plastic-coated pipelines can lead to substantial long-term savings. While the initial installation cost may be higher than that of conventional pipelines, the reduced maintenance and replacement costs make up for it over time. The durability of plastic coatings means fewer repairs and longer intervals between replacements, ensuring that your infrastructure remains both functional and financially viable.
3.3 Environmental Sustainability
As the world shifts towards more sustainable practices, plastic-coated pipelines offer a **greener** alternative. The materials used for plastic coatings are often recyclable, and their longevity reduces the need for frequent replacements, which in turn lowers the environmental impact of pipeline production and disposal. Additionally, the energy efficiency of these pipelines can contribute to reducing overall carbon footprints in industrial operations.
3.4 Improved Flow Efficiency
Plastic coatings can also enhance the **flow efficiency** of pipelines. The smooth surface of the plastic coating reduces friction, allowing fluids to flow more freely. This results in lower energy consumption for pumping systems and can facilitate better overall performance in transporting liquids or gases.
4. Applications of Plastic-Coated Pipelines
Plastic-coated pipelines find applications across various sectors, owing to their versatility and benefits.
4.1 Industrial Applications
In industrial settings, plastic-coated pipelines are widely used for transporting chemicals, water, and other fluids. Industries such as oil and gas, pharmaceuticals, and food processing benefit from the corrosion resistance and flow efficiency that these pipelines offer. The ability to withstand harsh conditions makes them ideal for critical infrastructure.
4.2 Municipal Applications
Municipalities increasingly rely on plastic-coated pipelines for water distribution and sewage systems. Their resistance to corrosion and lower maintenance requirements lead to improved service delivery and reduced costs for public utilities. Moreover, the environmental benefits align with the sustainability goals of many local governments.
5. Maintenance and Care of Plastic-Coated Pipelines
While plastic-coated pipelines are designed for durability, proper maintenance is still essential for optimal performance. Regular inspections should be conducted to identify any signs of wear or damage. Cleaning the exterior of the pipelines can help prevent the buildup of debris and contaminants that could compromise their integrity. Additionally, keeping an eye on the joints and connections ensures that any potential leaks are promptly addressed.
6. Choosing the Right Pipeline Systems
When selecting plastic-coated pipelines for your infrastructure, several factors should be considered. Assess the specific environmental conditions the pipelines will face, including temperature variations, chemical exposure, and pressure requirements. Consulting with experts in the field can provide valuable insights into the most suitable materials and coatings for your application.
7. Frequently Asked Questions
1. How long do plastic-coated pipelines last?
Plastic-coated pipelines can last for several decades, often exceeding 30 years, depending on the environment and maintenance practices.
2. Can plastic-coated pipelines be repaired?
Yes, plastic-coated pipelines can be repaired using specialized techniques, including patching or re-coating, to extend their lifespan.
3. Are plastic-coated pipelines safe for transporting drinking water?
Many plastic coatings are certified for direct contact with drinking water, making them safe for such applications.
4. How do plastic-coated pipelines compare to traditional metal pipelines?
Plastic-coated pipelines typically offer better corrosion resistance, lower maintenance costs, and improved flow efficiency than traditional metal pipelines.
5. Can plastic coatings be applied to existing pipelines?
Yes, existing pipelines can be retrofitted with plastic coatings to enhance their performance and extend their service life.
8. Conclusion
The use of plastic-coated pipelines represents a significant advancement in the protection and efficiency of industrial and municipal infrastructure. With their outstanding corrosion resistance, cost-effective maintenance, and environmental sustainability, these pipelines offer a robust solution for a wide range of applications. By choosing plastic-coated pipelines, organizations can safeguard their investments, reduce operational costs, and contribute to a more sustainable future. Investing in this technology is not just a trend; it's a strategic move towards enhancing the resilience and reliability of your infrastructure.
TAG:
Related Posts
Protect Your Infrastructure: The Comprehensive Benefits of Plastic-Coated Pipelines
Protect Your Infrastructure: The Comprehensive Benefits of Plastic-Coated Pipelines
Table of Contents
1. Introduction to Plastic-Coated Pipelines
2. What Are Plastic-Coated Pipelines?
3. Advantages of Plastic Coating in Pipelines
3.1 Corrosion Resistance
3.2 Cost-Effectiveness
3.3 Environmental Sustainability
3.4 Improved Flow E